Plant Manager - #443141
Hexion Inc.
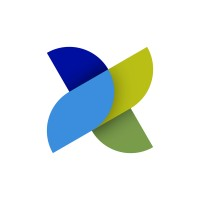
Imagine Everything. Build the Future with Hexion.
At Hexion, we push boundaries, rethink possibilities, and create real impact. We activate science to deliver progress—developing breakthrough solutions that strengthen industries, protect communities, and drive a more sustainable future.
This is where bold thinkers, problem-solvers, and innovators come together to shape what’s next. Whether you're engineering advanced materials, transforming manufacturing technologies, or leading strategic innovation, your ideas and actions leave a lasting mark. We cultivate an inclusive culture of growth, collaboration, and accountability, ensuring every contribution propels us forward.
We don’t follow the status quo—we challenge it, disrupt it, and improve it. Every role at Hexion is part of something bigger.
We invest in innovation, sustainability, and continuous development—equipping you with the tools, training, and opportunities to excel. With an unwavering commitment to safety, partnership, belonging, and impact, we empower you to lead change and strengthen industries worldwide.
This position is responsible for the safe and efficient operation of the total manufacturing operations of the Edmonton, Alberta site which consists of ~75 Hexion fulltime associates and an additional ~25-45 of contractors that fluctuate with work and projects. This role leads and directs all activities associated with safe-efficient plant activities including environmental, safety and health assurance, Operations, Logistics and Maintenance workforce. Facilitates efficiencies and coordination between key departments on site and corporate functions. Implements and aligns with Company policies including but not limited to safety, environmental, quality programs, and employee relations policies. Coordinates efforts between production areas and other business functions and represents as a key site within manufacturing in the North Region. Effectively leads the site and its people in alignment with overall business goals. Champions site Productivity projects that drive continuous improvement, cost and variability reduction.
Environmental, Health, and Safety
- Ensures site compliance with all safety, health and environmental laws, codes, and standards.
- Ambassadors and responsible for driving safety culture at the site.
- Provides leadership to the site and its personnel to drive continuous EHS improvement; demonstrates high visibility on the production floor driving improvements and accountability.
- Works with EH&S staff, develops and implements programs, processes, and procedures to ensure the safety and health of all associates working at the site. Ensures site support of EHS improvements.
- Ensures site operating guides are maintained and that site associate training is robust to ensure success.
- Develops and maintains a constructive relationship and dialogue between the site, the community, and local regulatory bodies as appropriate.
- Follows Process Safety Management standards and hazard recognition.
- Reviews all incident investigations, PHA’s, operator certification check sheets, annual procedure reviews, confided space permits and MOC documents.
Human Resource Management
- Establishes employee performance expectations and ensures they are met throughout areas of responsibility through performance reviews and direct feedback.
- Establishes and ensures implementation and adherence to training programs for site associates.
- Implements Company programs and policies and ensures adherence.
- Effectively communicates and aligns with Hexion/Site objectives.
- Models Hexion core values always.
- Talent champion in recruitment, development, and engagement.
- In compliance with local legislation.
- Corporate Governance: Ensuring transparency, accountability, and ethical decision-making at all levels of the organization.
Productivity/Cost/Finance
- Demonstrated financial acumen.
- Develops annual and multi-year budgets and plans targeting year after year performance improvement.
- Manages and measures cost performance and takes corrective cost control action.
- Develops, leads, and directs site productivity improvement programs and processes using Six Sigma tools, to drive resource optimization.
- Tracks and monitors all plant costs and explains adjustments and variances.
- Proven ability/experience leading and influencing teams, groups, and individuals.
- Excellent facilitation skills with a high level of energy that fosters engagement and teamwork.
- Excellent communication skills both written and verbal, and comfortable using workplace communications technology.
- Demonstrated ability to drive associate alignment, engagement, and accountability.
- Open to feedback for growth and development.
- Agile and flexible in approach to align with the needs of the company, clients, and associates.
Please Note: Candidate must have strong plant experience leading / managing a chemical manufacturing site. Candidates will not be considered for the role without demonstrated experience in a chemical environment.
- Experience in the chemical industry and focused experience with manufacturing products and processes in a PSM (process safety management) chemical manufacturing environment required.
- 15+ years total professional experience with 8+ years in a successful supervisory capacity (both staff and hourly) at a manufacturing site. Prior plant / site leadership experience preferred.
- Proven track record to sustain, change and embed safe operations within a plant environment and the associates.
- Demonstrated experience as a role model leading plant-based teams with strong safety performance while understanding the cultural elements required to instill a personal safety mindset.
- Demonstrated leadership experience and team building skills.
- Lean Six Sigma tools and Techniques to drive continual improvement and operational excellence. Includes 5S, Lean, Gemba, Leader Standard Work, Visual Management and KPI targets.
- Technical writing, math and statistical analysis and analytical problems solving skills.
- Maintenance and production optimization experience.
- Prior experience functioning as a project manager.
- Demonstrated ability to supervise and motivate a team, as well as the ability to work with and motivate peers and within teams.
- Significant experience with EHS to include working knowledge and practice of OSH, EPA, PSM.
Education Requirements
- Engineering undergraduate degree; Chemical Engineering, Mechanical, or Manufacturing is preferred.
How to apply
To apply for this job you need to authorize on our website. If you don't have an account yet, please register.
Post a resumeSimilar jobs
Oilfield Welders Needed in Grande Prairie, AB
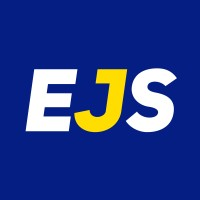
Butcher
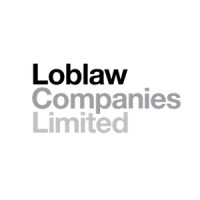
Training Coordinator (Trainer)
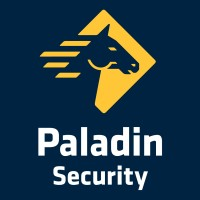